ATEX inspection checklist: What inspectors look for
Discover what to look for in an ATEX inspection in hazardous environments. Learn how EXTAGS simplify ATEX equipment tracking and safety.
When it comes to operating in potentially explosive environments, safety is essential. This is where ATEX inspections play a vital role. These inspections ensure that equipment and installations within hazardous areas meet strict safety standards.
So, what exactly do you need to look for during an ATEX inspection? Whether you are preparing for an audit or maintaining compliance, understanding the inspection process is essential.
In this blog, we will break down the key areas to focus on during an ATEX inspection, why regular checks are crucial and how tools like EXTAGS can simplify tracking and compliance for your ATEX equipment.
What are ATEX inspections and why do they matter?
ATEX inspections are critical and will help your organisation in demonstrating that all ATEX equipment is certified, has the right protection for potentially explosive environments and is safe to use.
Regular ATEX inspections are vital to ensure equipment is fit for purpose and compliant with regulations. If inspections are not carried out, it presents a huge risk of explosions and potential fatalities.
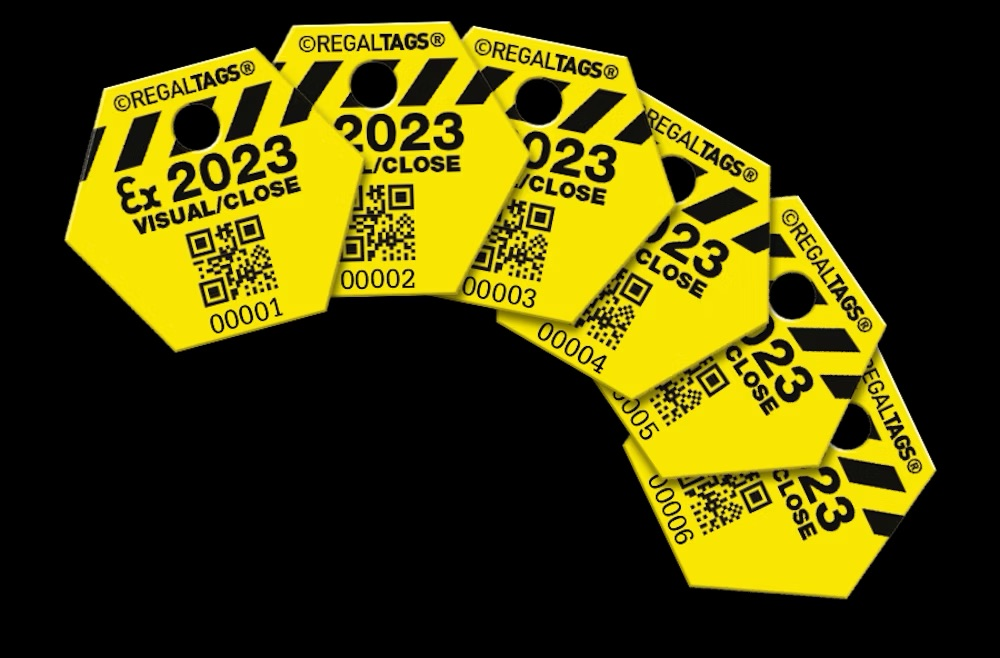
Key areas covered during an ATEX inspection
During an ATEX inspection there are some key areas that need to be covered, including:
1. Area classification: Understanding hazardous zones
A critical first step in any ATEX inspection is identifying and classifying areas where explosive atmospheres may occur. This involves assessing the presence and frequency of flammable gases, vapours, mists or dusts that could create an explosion risk. Areas are classified into zones based on the likelihood and duration of an explosive atmosphere.
Zones 0,1, 2: For gases and vapours
- Zone 0: Explosive atmosphere present continuously or for long periods.
- Zone 1: Likely to occur in normal operation.
- Zone 2: Not likely in normal operation or only for a short period.
Zones 20, 21, 22: For dusts
- Zone 20: Explosive dust atmosphere present continuously.
- Zone 21: Likely to occur occasionally.
- Zone 22: Not likely or only for a short period.
2. Equipment suitability and correct marking
All equipment intended for use, whether they are electrical or non-electrical, must be compliant. This includes, but is not limited to:
- Lighting
- Generators
- Machinery
- Ventilation systems
- Protective systems
- Control panels
There are 3 critical reasons why your equipment needs to be inspected regularly:
- Employee safety: Personnel working in ATEX areas are the most at risk in the event of an accident. It is crucial that all tools and equipment they are working with are as safe as possible.
- Site protection: It only takes a small spark from a defective piece of equipment to cause a catastrophic explosion. This can cause major problems on a section or the entirety of your facility.
- Legal compliance: There are two ATEX directive laws in the UK under DSEAR and EPS regulations that you need to comply with. Failure to comply can lead to substantial fines and even the suspension of business operations.
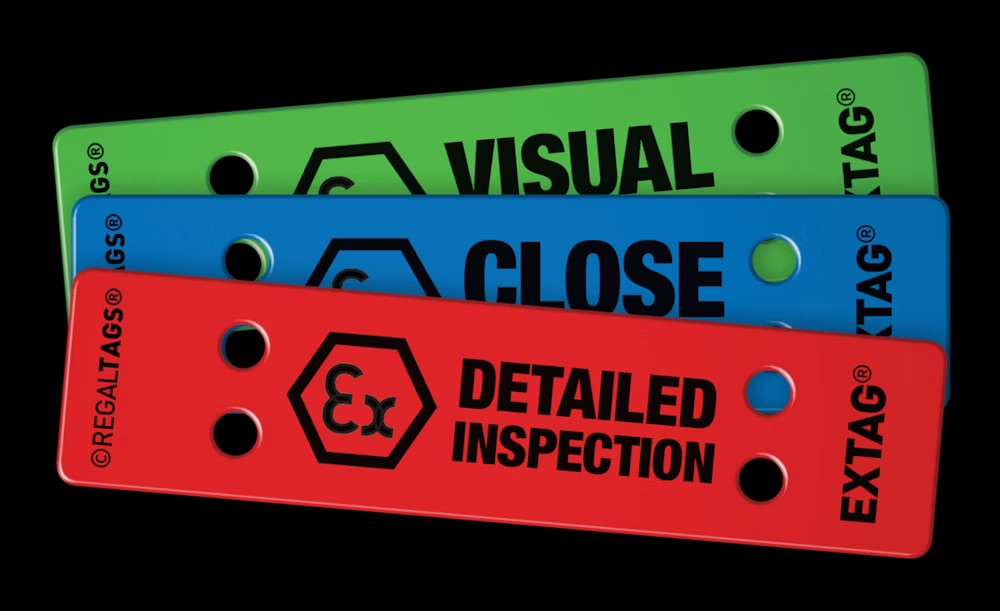
3. Physical condition and installation checks
When inspecting, you will need to thoroughly assess the physical state of all apparatus and installations. This includes checking that the equipment is appropriate for the classified area, ensuring there are no visible unauthorised modifications and verifying that all bolts, cable entries and blanking elements are of the correct type, complete and tightly secured.
While assessing, also check for obvious damage to cables, confirm that sealing of ducts, pipes, and conduits is satisfactory, and ensure earthing connections are secure and of sufficient cross-section. The integrity of enclosures, gaskets, and other protective features is also evaluated to confirm they remain effective and undamaged.
4. Protection against ignition sources
A critical part of the inspection is identifying and controlling potential ignition sources. Check for risks such as open flames, hot surfaces, electrical sparks and static electricity.
Only certified ATEX-compliant equipment may be used in hazardous areas, and all measures must be in place to eliminate ignition sources.
5. Environmental protection measures
Upon examining, you will need to verify that all apparatus is adequately protected against environmental factors such as:
- Corrosion
- Weather
- Dust accumulation
- Vibration
Check for the absence of undue dust and dirt buildup, confirm that protective coatings or enclosures are intact and ensure equipment is suitable for the specific environmental challenges of the location.
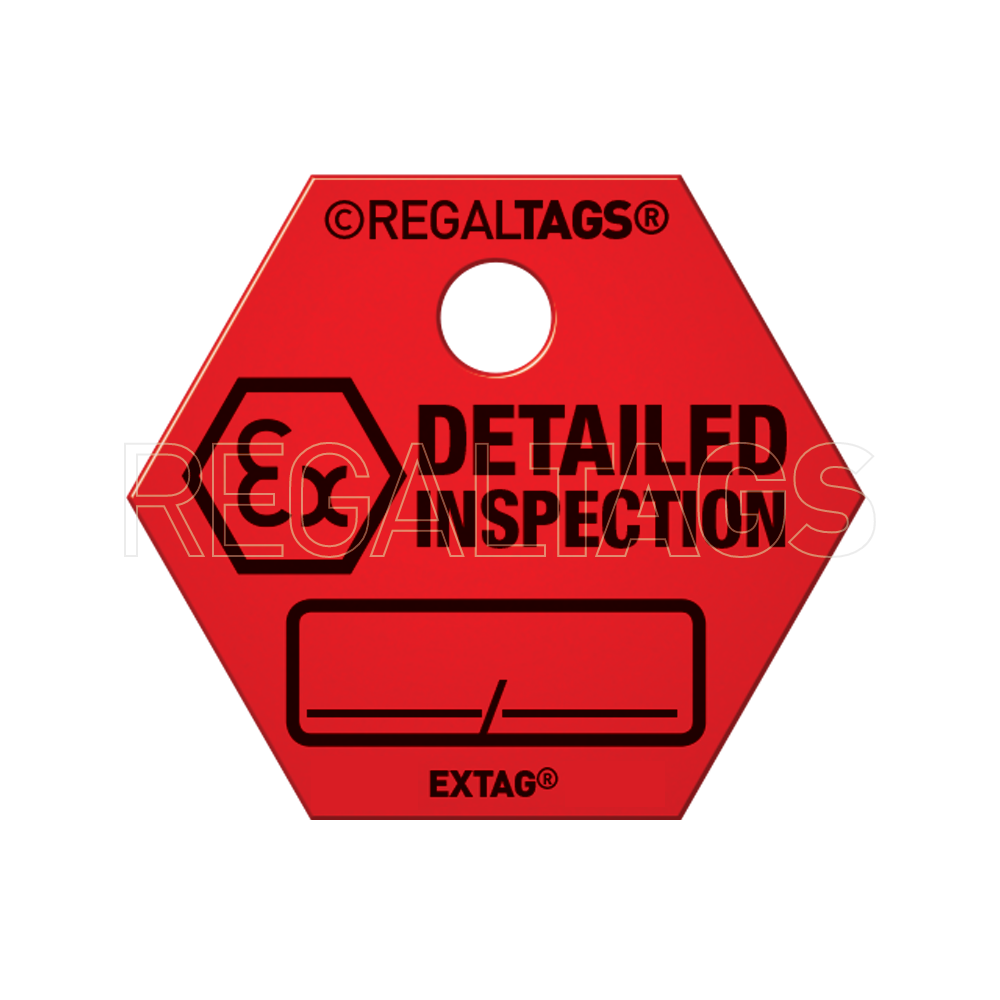
6. Documentation, records and compliance
A thorough review of documentation is essential. Ensure that up-to-date records are maintained for all ATEX equipment, including certification documents, technical files, and maintenance logs.
Compliance with ATEX legislation requires a technical file for each piece of equipment, including declarations of conformity and evidence that all apparatus meets the required standards.
7. Testing and maintenance requirements
Regular testing and maintenance are key to ongoing safety and compliance. Check that all required inspections have been performed according to schedule.
You will need to verify that maintenance activities are documented, that any defects have been addressed, and that equipment continues to meet ATEX standards throughout its lifecycle.
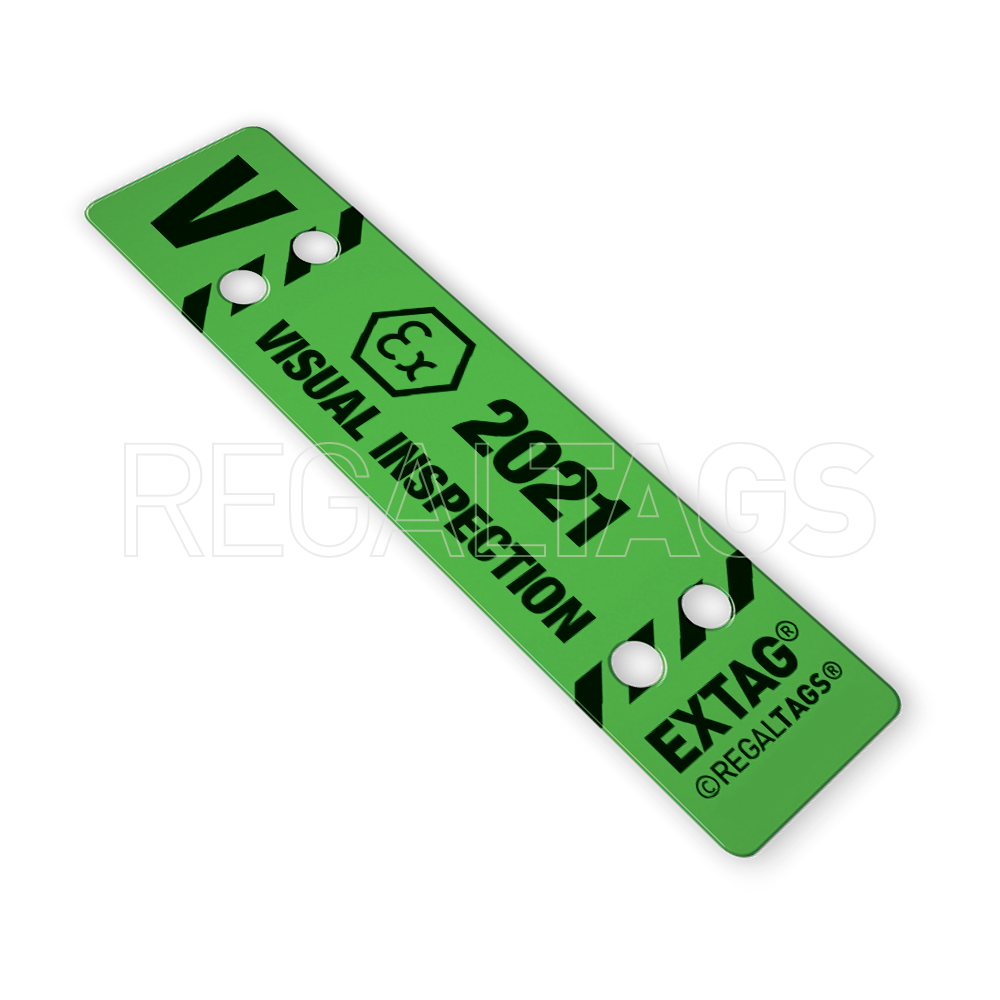
How EXTAGS help you track and manage ATEX equipment
EXTAGS® are highly visual inspection tags specifically designed for identifying and tracking the Ex-inspection status of equipment in ATEX environments. Their key benefits include:
- Instant visual identification: EXTAGS use clear colour coding and text to indicate the degree of inspection, such as ‘Visual’, ‘Close’ or ‘Detailed’, making it easy for inspectors and workers to see the inspection status immediately. Even on equipment located in high or hard to reach areas.
- Durability in harsh environments: Manufactured from UV and freeze-resistant Prism Polypropylene, EXTAGS are built to withstand the challenging conditions typical of hazardous areas. This ensures that inspection information remains legible and intact over time.
- Customisation and traceability: EXTAGS can be fully customised in colour and design to suit specific site requirements. They are available with QR codes, barcodes and unique sequential numbering. This supports digital tracking and ultimate traceability of inspections.
- Integration with inspection software: By incorporating QR codes or barcodes, EXTAGS can be linked to inspection management software. This allows real-time recording and central monitoring of inspection data for every tagged item.
- Efficient equipment management: The visual system helps teams quickly identify which items need inspection or maintenance, reducing the risk of missed checks and improving overall compliance with ATEX safety regulations.
EXTAGS streamline the process of tracking, inspecting and managing ATEX equipment, supporting both operational efficiency and regulatory compliance in hazardous environments.
Prepare for your ATEX inspections with REGALTAG
At REGALTAG, we help companies working in the harshest environments around the globe with customised safety tagging solutions.
If your organisation is looking for a reliable solution to support your critical operations, we can help. Contact our team of experienced advisors today.
Subscribe
Join 18,000+ others receiving our monthly updates. Free Tag insights delivered straight to your inbox.